PROCESS
Unlimited challenges through innovation
Process
MANUFACTURE PROCESS
Main product manufacturing process

PROCESS 01.
MATERIAL

PROCESS 02.
FORGING

PROCESS 03.
CUTTING PROCESS

PROCESS 04.
QUALITY INSPECTION

PROCESS 05.
SHIPMENT / DELIVERY
PROCESS 01.
MATERIAL
MATERIAL

The metal cutting industry produces a very wide range of components from a variety of materials. Each material has unique properties, and these properties are affected by alloy composition, heat treatment, hardness, etc. This influences the choice of cutting tool geometry, grade and cutting conditions. To make selection easier, workpiece materials are divided into six main groups based on ISO standards, each with its own unique processing characteristics.
PROCESS 02.
FORGING
FORGING

Forging is the process of heating metal to a certain temperature and then applying force to create a certain shape. Forging is one of the oldest forming methods. Forging is an operation to shape a solid metal material into a certain shape by mechanically hitting it with a hammer or pressurizing it.
Forging is a type of plastic processing. The metal workpiece is struck with a hammer, etc. to form it into the desired shape. Its characteristic is that it has strong properties (toughness) against impact because the material is tougher than processing through casting or powder metallurgy. Forging is used in the manufacture of tools, tableware, automobiles, and railroad parts. For forging, the beating temperature may be room temperature, but for materials with a high melting point, some heating is often required. In general, forging at a temperature higher than the temperature at which recrystallization occurs in the material is called hot forging, forging above the recrystallization temperature is called warm forging, and forging above the recrystallization temperature is called warm forging. Forging at high temperature is called cold forging. The operation of hitting with a hammer to make the structure of a solid material uniform and to reduce the size of the crystal grains in crystalline solids is called tempering. It is made into a predetermined shape by gradually pressing with a tool rather than hitting with a hammer. Work is called press.
Forging is mainly used for iron. Iron has the property of combining two red-hot pieces by hitting them with a hammer, and by hitting them repeatedly, they are tempered and become stronger. A sword is a representative example. Today, it is mechanized, such as forging. Chugeum (鎚金) is a technique of forming a plate of a highly malleable material such as gold, silver, copper, or iron by placing it on a danggeum (ambil - a supporting metal lump) and hitting it with a sledgehammer to stretch or squeeze it. It was widely used in everyday utensils such as weapons, religious utensils, and vessels. Today, mass production technologies are being developed, such as press, which processes sheet metal by placing it between molds and applying pressure, and spinning, which deforms sheet metal attached to a rotating shaft by rotating it. It occupies a major part of recent metal products such as automobile bodies, dishes, and lighting fixtures.
Forging is a type of plastic processing. The metal workpiece is struck with a hammer, etc. to form it into the desired shape. Its characteristic is that it has strong properties (toughness) against impact because the material is tougher than processing through casting or powder metallurgy. Forging is used in the manufacture of tools, tableware, automobiles, and railroad parts. For forging, the beating temperature may be room temperature, but for materials with a high melting point, some heating is often required. In general, forging at a temperature higher than the temperature at which recrystallization occurs in the material is called hot forging, forging above the recrystallization temperature is called warm forging, and forging above the recrystallization temperature is called warm forging. Forging at high temperature is called cold forging. The operation of hitting with a hammer to make the structure of a solid material uniform and to reduce the size of the crystal grains in crystalline solids is called tempering. It is made into a predetermined shape by gradually pressing with a tool rather than hitting with a hammer. Work is called press.
Forging is mainly used for iron. Iron has the property of combining two red-hot pieces by hitting them with a hammer, and by hitting them repeatedly, they are tempered and become stronger. A sword is a representative example. Today, it is mechanized, such as forging. Chugeum (鎚金) is a technique of forming a plate of a highly malleable material such as gold, silver, copper, or iron by placing it on a danggeum (ambil - a supporting metal lump) and hitting it with a sledgehammer to stretch or squeeze it. It was widely used in everyday utensils such as weapons, religious utensils, and vessels. Today, mass production technologies are being developed, such as press, which processes sheet metal by placing it between molds and applying pressure, and spinning, which deforms sheet metal attached to a rotating shaft by rotating it. It occupies a major part of recent metal products such as automobile bodies, dishes, and lighting fixtures.
PROCESS 03.
CUTTING PROCESS
CUTTING PROCESS
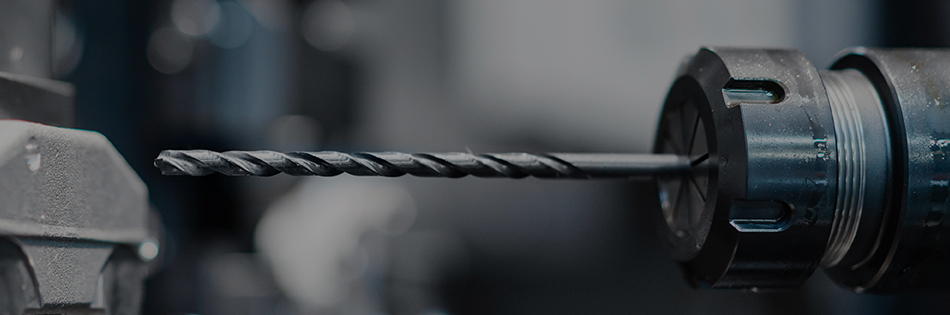
Cutting process is a technology that creates a desired shape, such as cutting or drilling a hole, by moving a material (workpiece) such as metal and a tool relative to each other. Cutting processing is largely divided into two types: turning, which rotates the tool while fixing the workpiece, and turning, which rotates the workpiece itself. There is milling as a representative of turning, and lathe as a representative of turning.
Cutting is a technology that uses tools to cut and process materials such as metal. General materials, forgings, or castings are cut into desired shapes and dimensions to create products. This is a processing method that uses a machine tool to cut and cut a workpiece into the desired shape and dimension. The optimal cutting speed is selected depending on the type or material of the tool and is divided into rough cutting and finished cutting depending on the finishing allowance. Heat treatment after cutting requires grinding processing. Simply defined, cutting processing refers to a processing technology that processes materials such as metal or plastic by cutting or drilling holes using machine tools. The workpiece is cut into the shape shown in the drawing using a machining center, NC lathe, or 5-axis processing machine. Since cutting processing is performed by contacting a tool or workpiece rotating at high speed with a machine, it is necessary to pay attention to the management of resistance due to friction, rotation speed, and temperature.
Types of cutting processing include turning, which involves cutting the outer diameter, inner diameter, cross section, and threads of a cylinder using a lathe, drilling holes with a drilling machine, super pennissing, reaming using a reamer, and cutting internal threads using a tap, etc. Hole drilling (tapping), boring to make precise holes with a boring machine, planing to machine a plane or groove with a planer, slotting to machine a key groove on a shaft with a slotter, and flat and curved surfaces with a milling machine. , milling to process faces, grooves, etc., shaping to process small-area surfaces or grooves with a shaper, broaching to process key grooves and spline grooves with a broaching machine, and gear cutting to process gear wheel teeth with a gear cutting machine. , cutting processing using a sawing machine, etc. Cutting processing basically requires cutting motion, feed motion, and positioning motion.
Cutting is a technology that uses tools to cut and process materials such as metal. General materials, forgings, or castings are cut into desired shapes and dimensions to create products. This is a processing method that uses a machine tool to cut and cut a workpiece into the desired shape and dimension. The optimal cutting speed is selected depending on the type or material of the tool and is divided into rough cutting and finished cutting depending on the finishing allowance. Heat treatment after cutting requires grinding processing. Simply defined, cutting processing refers to a processing technology that processes materials such as metal or plastic by cutting or drilling holes using machine tools. The workpiece is cut into the shape shown in the drawing using a machining center, NC lathe, or 5-axis processing machine. Since cutting processing is performed by contacting a tool or workpiece rotating at high speed with a machine, it is necessary to pay attention to the management of resistance due to friction, rotation speed, and temperature.
Types of cutting processing include turning, which involves cutting the outer diameter, inner diameter, cross section, and threads of a cylinder using a lathe, drilling holes with a drilling machine, super pennissing, reaming using a reamer, and cutting internal threads using a tap, etc. Hole drilling (tapping), boring to make precise holes with a boring machine, planing to machine a plane or groove with a planer, slotting to machine a key groove on a shaft with a slotter, and flat and curved surfaces with a milling machine. , milling to process faces, grooves, etc., shaping to process small-area surfaces or grooves with a shaper, broaching to process key grooves and spline grooves with a broaching machine, and gear cutting to process gear wheel teeth with a gear cutting machine. , cutting processing using a sawing machine, etc. Cutting processing basically requires cutting motion, feed motion, and positioning motion.
PROCESS 04.
QUALITY INSPECTION
QUALITY INSPECTION

Quality control seeks to maintain and improve quality by using statistical methods in production management to discover the causes of defective products and eliminate them. In other words, quality control refers to preventing as much as possible the causes of defective products during the manufacturing process.
PROCESS 05.
SHIPMENT / DELIVERY
SHIPMENT / DELIVERY

In the product shipping stage, the completed manufactured product is shipped to the customer. We plan packaging and transportation, select appropriate packaging materials to protect the product, and pay careful attention to ensuring that the product is safely delivered to customers.